1. 工业转型的瓶颈,靠“虚拟预演”能突破吗?
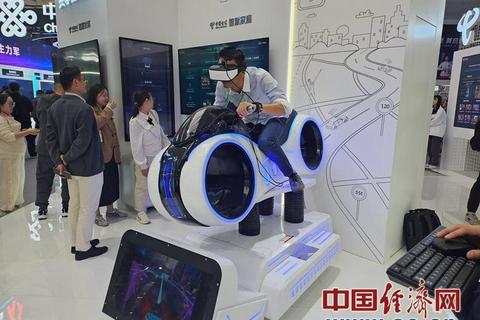
当德国大众2025年工厂蓝图曝光时,一组对比数据引发行业震动:使用传统试错法调试汽车焊接机器人需6个月,而通过NVIDIA Omniverse平台进行数字孪生测试仅需3周。这不禁让人思考:面对个性化制造与柔性生产的产业浪潮,传统工业模式是否已触及天花板?
全球制造业正面临双重挤压——熟练技工缺口达7700万人(国际劳工组织2023年数据),而产品迭代周期却缩短了40%。在这样的矛盾中,“智能驱动·沉浸式体验:机器人仿真软件赋能未来工业新生态”开始展现颠覆性力量。美国ABI Research预测,到2027年工业仿真市场规模将突破210亿美元,其中机器人仿真占比超35%。
2. 算法能否替代千万次物理测试?
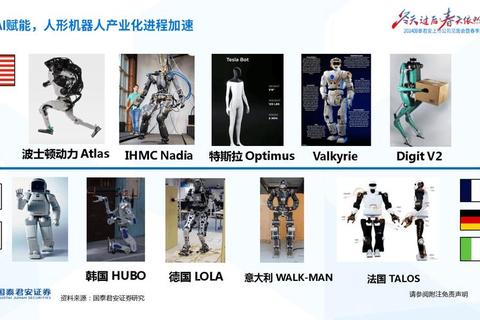
富士康深圳工厂的案例极具说服力。在为某手机品牌开发自动化装配线时,工程师利用Visual Components软件创建了包含137台机器人的虚拟车间。通过20万次碰撞检测模拟,成功将产品切换时间从72小时压缩至8小时,缺陷率降低62%。这印证了“智能驱动·沉浸式体验:机器人仿真软件赋能未来工业新生态”的核心价值:用数字世界的无限试错,替代物理世界的昂贵实验。
更值得关注的是算法进化带来的质变。波士顿动力将强化学习算法融入仿真系统后,四足机器人Spot的越障训练效率提升400倍。这种“虚拟进化”机制,使得机器人能在48小时内掌握人类工程师需要半年调试的复杂动作。
3. 人机协作的边界在哪里重构?
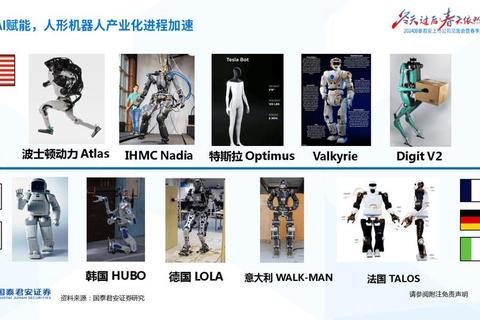
日本发那科的实践给出了新思路。其开发的AR+仿真系统,让操作员通过Hololens眼镜实时查看机器人运动轨迹,在汽车焊装车间将人机协作效率提升55%。这揭示出“智能驱动·沉浸式体验:机器人仿真软件赋能未来工业新生态”的深层逻辑:不是取代人类,而是创造“数字纽带”。
医疗机器人领域更凸显这种协同价值。直觉外科公司通过仿真软件预演达芬奇手术机器人操作,成功将前列腺切除手术精度提升至0.1毫米级,术后并发症发生率降低34%。当算法能模拟2000种突发状况时,人类专家的决策质量反而得到增强。
4. 生态重构需要跨越哪些现实鸿沟?
尽管成效显著,但产业调研显示:73%的中小企业仍受困于仿真人才短缺。东莞某家电企业的转型之路颇具代表性——引入RobotStudio仿真平台后,虽将新品研发周期缩短40%,却因缺乏数据解析能力,导致30%的模拟结果未能有效转化。
这指向“智能驱动·沉浸式体验:机器人仿真软件赋能未来工业新生态”落地的关键:需建立“技术-人才-流程”的三角支撑。海尔智家构建的仿真工程师认证体系值得借鉴,通过将3D视觉编程等技能拆解为52个标准化模块,半年内培养出200名复合型人才。
行动路线图
1. 技术嫁接:分阶段引入开源框架(如Gazebo),逐步对接MES/ERP系统
2. 人才孵化:与职业院校共建“数字双胞胎实训中心”,开发模块化课程
3. 数据闭环:建立“仿真预测-实体验证-算法优化”的迭代机制,尤其关注能耗与安全参数的校准
4. 生态共建:参与行业标准制定(如ISO 23218),推动仿真模型跨平台兼容
当德国库卡利用仿真技术实现生产线“热切换”(不停机改造)时,节省的每度电都在重写工业规则。这提醒我们:未来的制造竞争力,正取决于企业在数字与现实世界间架设桥梁的能力。那些率先拥抱“智能驱动·沉浸式体验:机器人仿真软件赋能未来工业新生态”的企业,终将在不确定性中掌握进化的密钥。